A year after opening a $28.5 million factory, Seattle-based EnerG2 is looking like a textbook example of laboratory innovation in a strategically important industry generating U.S. high-tech manufacturing jobs, with an assist from Uncle Sam.
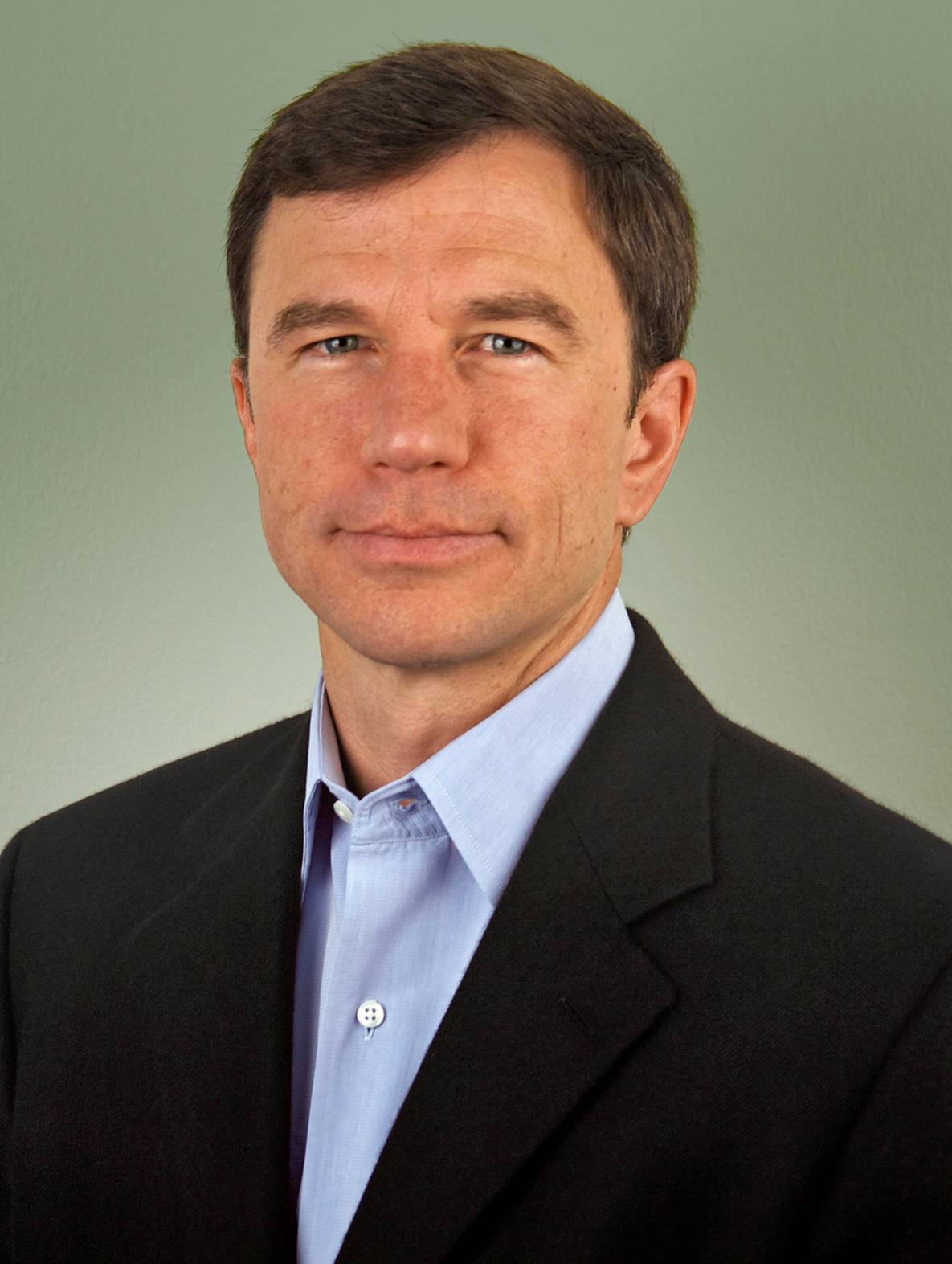
Someone page Joe Biden.
The company got a $21.3 million Department of Energy stimulus grant covering three-quarters of the cost to build a 72,000-square-foot facility in Albany, OR. It opened about a year ago and is now capable of producing tens of tons a month of high-surface-area activated carbon that can be “tuned” for a range of energy storage applications. That works out to enough material each year for about 60,000 electric cars, though output varies with customer demand.
EnerG2 isn’t saying anything about how much revenue it is generating or whether it is profitable, so don’t break out the champagne just yet. Backed to the tune of $24 million in venture capital over the last five years—including a $9.4 million round raised late last year— the company has about 50 employees, split between headquarters and R&D in Seattle, and manufacturing in Albany, where more of the growth is occurring as manufacturing output ramps up.
Co-founder and chief executive Rick Luebbe says EnerG2 now has relationships with more than 100 companies—some in the Fortune 50. Some companies are still testing its materials, while others are exploring product development partnerships, or have become paying customers for one of its two commercial products: high-purity activated carbon used in ultra capacitors, or as an additive to lead-acid batteries to improve their performance in the type of duty cycles seen in hybrid vehicles.
“We have a relatively long list of customers engaged for both systems,” Luebbe says, though they are skittish about being named. “When they recognize the competitive advantage, they don’t want their competitors to know how they’re getting it.”
The company has just completed the International Organization for Standardization‘s quality management certification, which Luebbe says will accelerate a change in perception that has benefitted EnerG2.
“We have observed—and it should have been obvious—that customer engagement radically shifted when the factory came on line and there was confidence in our ability to produce,” Luebbe says. The ISO9001 certification “shows the world our manufacturing facility is set up in a way to support long-term customer projects.”
EnerG2′s story, which we’ve tracked through the last several years, starts at the University of Washington, where co-founder Aaron Feaver was completing his PhD work in 2003 on a “carbon technology platform,” initially envisioned as a storage solution for hydrogen and later methane.
Those markets were slow to develop, and EnerG2 might still be waiting had it not turned its attention in 2006 to electricity storage.
The platform uses commodity organic chemicals in a controlled polymerization reaction—a derivation of the sol-gel process, for the materials science experts—to create a polymer subsequently processed into high-surface-area activated carbon with specific properties that can be optimized for different energy storage applications.
“We can change the molecular structure by changing the fundamental organic chemicals, catalysts, ratios, and reactions,” Luebbe explains. “There are lots of levers to toggle to get very different structures.”
The same technology platform can be applied to the company’s manufacturing infrastructure to produce activated carbon with attributes such as surface area, density, and pore structure, size distribution, and volume tuned for specific battery chemistries, or to store other energy sources such as methane.
EnerG2 believes its advantage lies not only in the purity and “tunability” of its carbon relative to organic feedstocks such as coconut shells, but also in the opportunity to apply this platform to multiple end markets. Other carbon suppliers tend to be focused on a single application, Luebbe says.
“We’re taking an R&D platform and turning it into a manufacturing capacity really we don’t see anywhere else in the world,” says co-founder and chief operating officer Chris Wheaton.
The scale-up has presented challenges Wheaton says are normal for manufacturers. But in one key respect, the process has been a positive surprise.
“You might expect to see a degradation in quality from the lab to manufacturing environment,” Wheaton says. “We’ve seen, at the very least, an equivalent performance in migrating from lab to plant. We can count on lessons learned in the lab to be true in the plant itself.”
That’s important as the company looks to its next phase of growth.
EnerG2 is moving into materials for other electrochemical storage systems that Luebbe says offer significant performance and cost improvements. Carbon anodes used in place of graphite in lithium ion batteries offer 50 percent higher capacity, faster charging rates, and longer life, Wheaton says.
Carbon is an ingredient in other battery chemistries including lithium sulfur and lithium air.
And with the North American natural gas boom, EnerG2 is again exploring this potential market.
“We get a call a week from somebody, some company, looking at absorbed natural gas systems for all kinds of different applications,” Luebbe says. “We think we have a differentiated material there that allows us to optimize specifically for storage of methane molecules.”
Absorbed natural gas (ANG) offers several advantages over compressed natural gas, Luebbe says, including safety and cost because ANG can achieve liquid-like storage densities at much lower pressure.
“We’re waiting for the industry to develop tank systems to hold carbons and integrate with vehicles,” he says, noting that Brookhaven National Laboratory demonstrated such systems a decade ago, but no one has commercialized the concept.